Plastic Product Gate system-gate design standard
1.1: Description of gating system lap / side gate design criteria
Side gate advantage:The pressure loss is the smallest and the product is the easiest to fill .
Side gate disadvantage :There will be obvious gate marks left , when trimming the gate, affecting the surface appearance.
Common molding defects of side gate :
1.Cold material near the gate
2.There are shrinkage marks near the gate
3.There are splayed whiskers near the gate
The side gate is often used for PP material. the material with cold material defects in the side gate is ABS/PC-ABS .
1.2 : Refer to the following figure for the specific gate size
1.3 : Specific case share
We suggest that this type of gate design is preferred for PP material, which can optimize the injection molding
defects often encountered by PP material, such as shrinkage near the gate, strain, splayed beard...
1.4: The stability of the gate type is verified by mold flow analysis
2. Description of gating system sub-gate design criteria
Sub-gate advantage:Realize production automation, small gate trace, and optimize common defects such as spray mark and gas mark.
Sub-gate disadvantage :The gate is difficult to process, with large pressure loss, relatively complex structure and easy to break. It is not suitable for materials with strong rigidity, such as PA, PS, AS and so on.
For ABS products with high requirements for appearance parts, pc-abs mostly adopts latent gate.
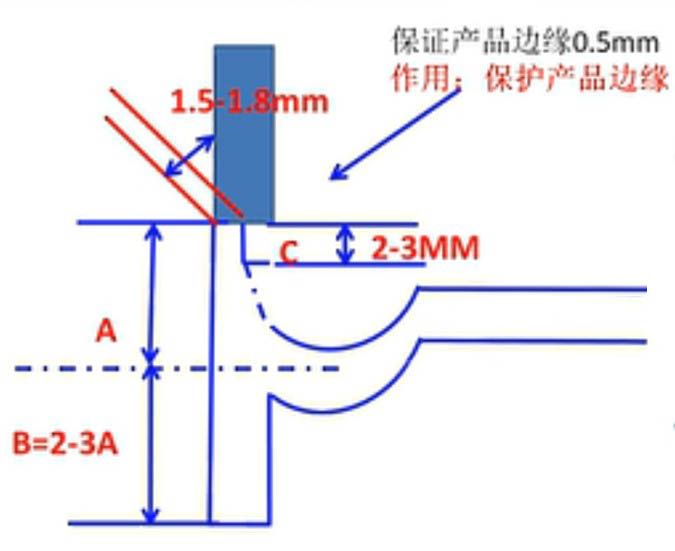
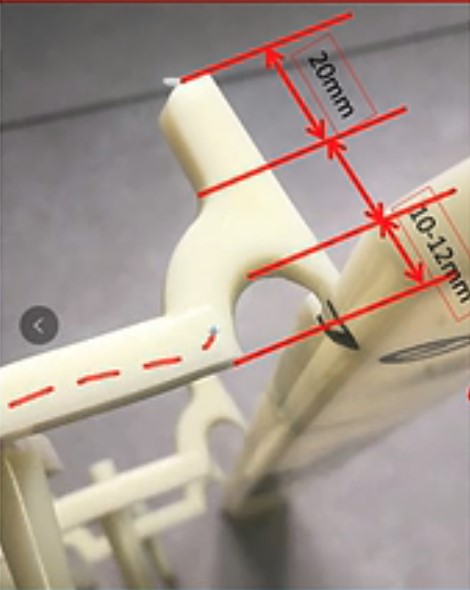