Solution to bubbles in injection molded parts – PC transparent products
Firstly, the causes of bubbles are analyzed.
There are two kinds of bubbles: thick transparent injection molded parts often leave bubbles in the central part.
There are two kinds of bubbles, one is the bubble caused by trapped gas, and the other is the vacuum bubble caused by product shrinkage.
Bubbles are generated because the injection speed is too fast, and the plastic flow cannot force all the air in the mold cavity to be discharged from the exhaust slot. The air mixes into the plastic to form bubbles.
Countermeasures: sufficient exhaust slots, especially at the end of main flow channel and product flow end; Using slow, fast and slow injection speed can avoid bubbles.
Vacuum bubble: it is caused by the shrinkage of thick plastic products when they are cooled. The surface wall of the mold cavity is cold, the outer wall of the product cannot shrink, and the center shrinks to form a vacuum bubble.
It can often be found that the center of the hot product just out of the mold is clean and free of bubbles, but bubbles (vacuum bubbles, shrinkage cavities of parts) appear after a period of time .
Phenomenon: the product cavity can be seen from the appearance .
Reasons: During the cooling process of the mold, due to insufficient mold filling and rapid cooling of the product surface, the workpiece shrinks from inside to outside to form a "vacuum bubble“
Countermeasures:
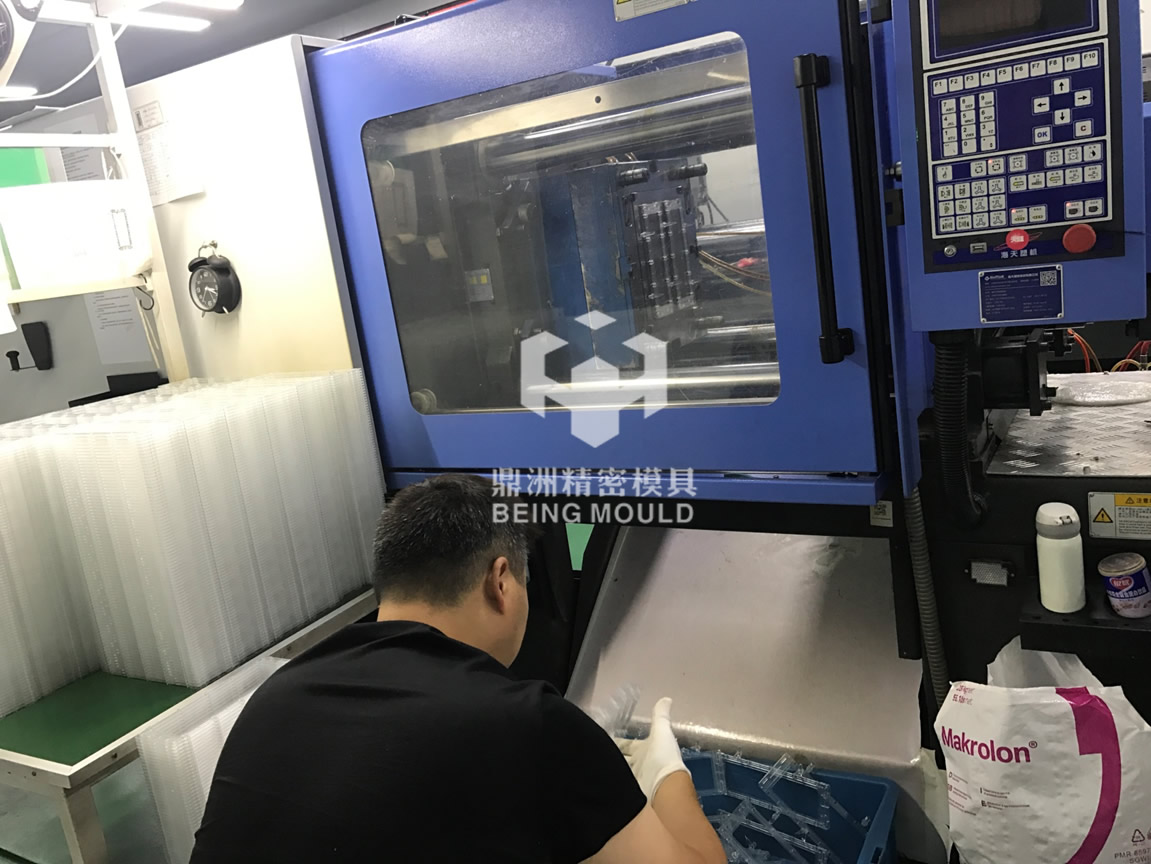
Share to: