Steps and considerations of plastic mold design
Plastic mold design is based on correct plastic product design. mold design and manufacturing are closely related to plastic processing. the success or failure of plastic processing largely depends on the effect of mold design and mold manufacturing quality. the structural elements to be considered in plastic mold design include:
Mold structure design
1、 The balance of the gating system. In the design of multi cavity mold, all cavities should be fed at the same time as much as possible. Due to the increase of the number of cavities, the length of the shunt channel must increase. Before the melt reaches the cavity, there will be a large loss of injection pressure and melt heat. If the design of the shunt channel is slightly unreasonable, there may be defects in the plastic parts, such as the dissatisfaction of one cavity or several cavities, Or live full immediately, but there are defects such as poor fusion or loose internal tissue. If the injection pressure is increased, it is easy to produce flash. The design runner in this paper is arranged in a non-equilibrium way. By setting the size of the gate and shunt channel, the injection process is adjusted to the value to ensure that the shrinkage of each cavity is the same, and the plastic parts with the highest precision requirements are interchangeable. The gate is set at the thick end of the plastic part, marked as the Y end, which is conducive to flow and feeding, and can also avoid welding marks, The molecular orientation can meet the requirements of bending without fracture.
2、 Design of cooling system the design principle of this cooling device is to design the cooling device without increasing the structure of the die itself. On the premise of meeting the transmission area required for cooling and the allowable die structure, the number of cooling circuits shall be designed as much as possible, and the cooling channel aperture shall be as large as possible. Cooling water holes shall be processed on the upper and lower cavity plates and dynamic fixed templates, During installation, the cooling water holes of the upper cavity plate are connected with the water holes of the fixed template, and then sealed with a sealing ring. The cooling water holes of the lower cavity plate are connected with the water holes of the moving template, and also sealed with a sealing ring. The water holes are arranged on the upper and lower cavity plates and the moving template.
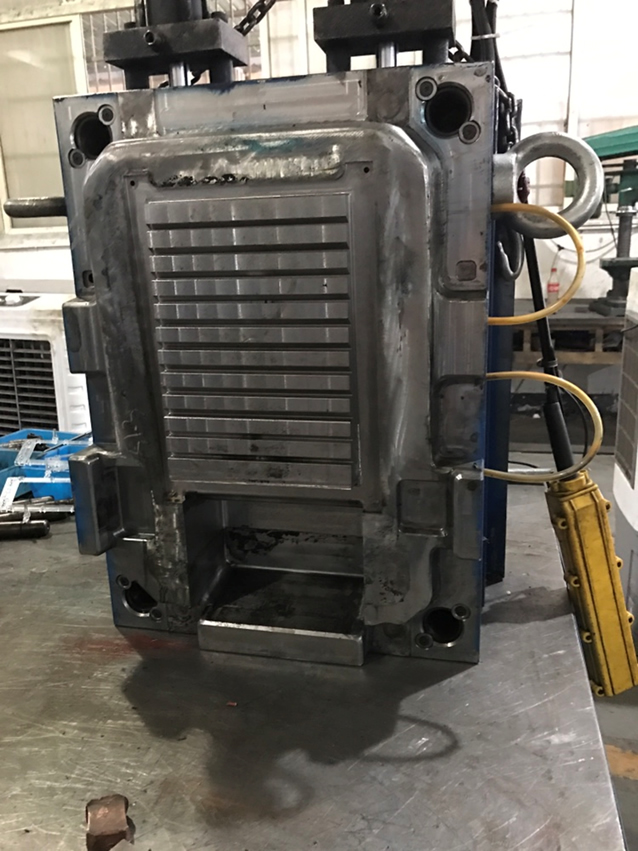