Why do injection mold design need insert design ?
1. Save
injection mold manufacturing materials
As we all know, injection molds use
regular block steel with fixed shape to fix materials, but the materials of
front and rear molds are determined by height. If one place is higher than
others, inserts can be made to reduce the height of the mold.
2. Convenient mold modification
Where the injection mold is often
modified, it can be removed and made into inserts. When changing the mold in
the future, as long as the inserts are replaced, and even when opening the
mold, several more inserts can be replaced, so as to facilitate the
modification of the mold.
3. Conducive to injection mold exhaust
The exhaust of injection mold is very
important. If the exhaust is not good, there will be trapped gas in the mold
cavity, especially in the relatively deep rib position. During injection
molding, the product is prone to bubbles or shrinkage, lack of glue, whitening
or black spots. Therefore, the insert can be added where the die needs to be
vented, and the matching gap of the insert can be used for venting.
4. Convenient injection mold processing
There are some deep rib positions in the
injection mold, which are difficult to be processed by the tool. Although EDM
can be used, the EDM processing speed is slow and the processing efficiency is
not high. Therefore, it is generally selected as an insert to reduce the
processing difficulty and facilitate exhaust. In addition, it is the deep
reinforcement mold matching, because the mold matching where the mold must be
matched is very inconvenient, but it is much more convenient to open the
inserts and disassemble and assemble in these places.
5. Extend the service life of injection
mold
Generally speaking, the place where the injection mold needs to design the insert is often the place easy to be damaged in the mold. Once the insert is damaged, it can be replaced, so as to prolong the service life of the injection mold and save time and money.
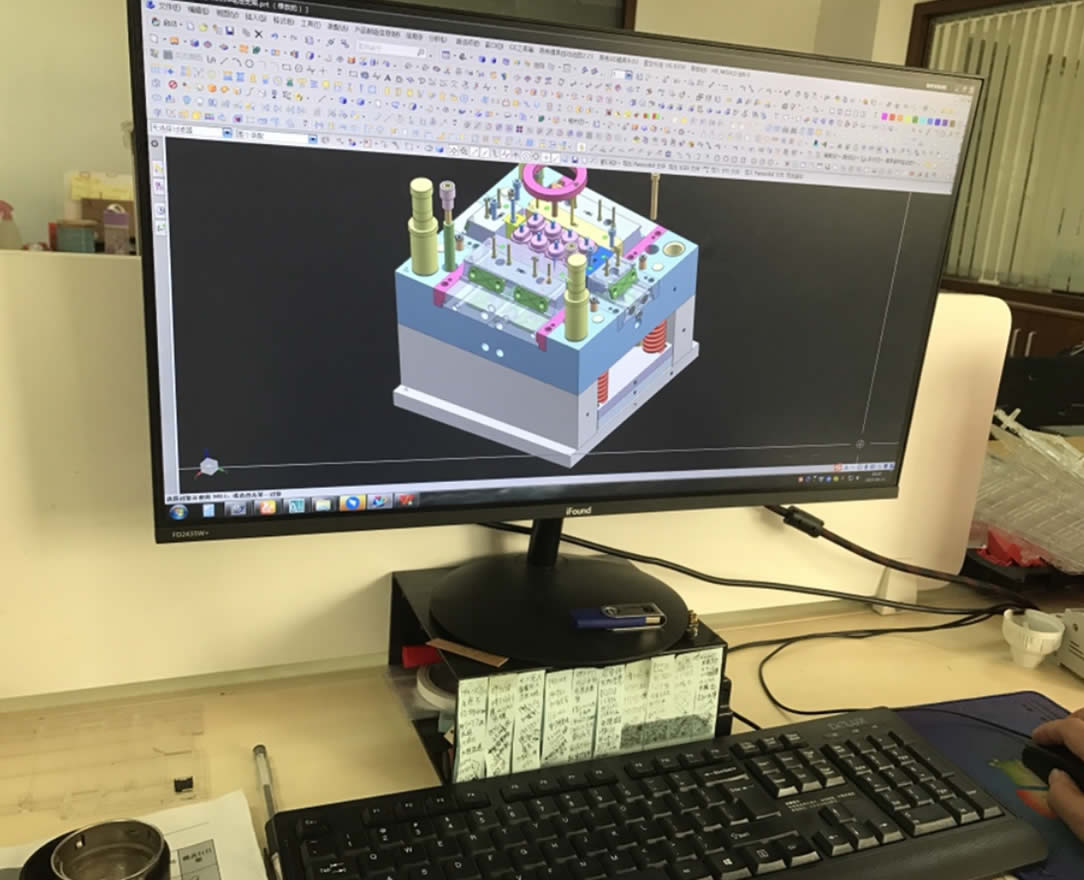
Share to: